Food Plant Resistive Touchscreen Panels
Resistive touch is probably one of the oldest technologies and still unbeatable in the right application. The resistive touchscreen started life in the ’70s and was an invention of Dr G Samuel Hurst originally called Elographics. It was made of a cover sheet with an X and Y axis which when pressure-activated resulted in the flow of electrical conductivity.
Elographics formed the foundation of the resistive touch panel that we know today. However, as technology has become more advanced and sophisticated, so to have resistive touchscreen panels. Indeed, modern touch panels consist of a top layer suspended by micro-dots and a bottom substrate (usually made of glass). When pressure is applied to the top layer, it pushes against the bottom layer, causing a signal to be transmitted back to the controller via a series of wires. This acts as a reference to the point touched on the screen.
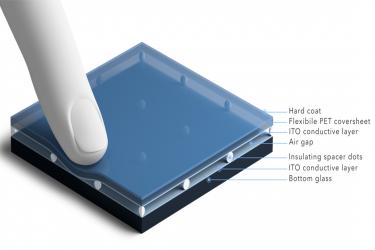
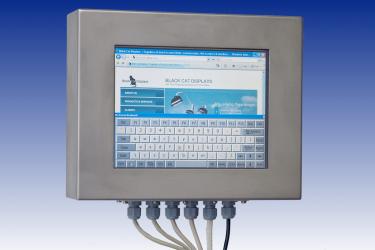
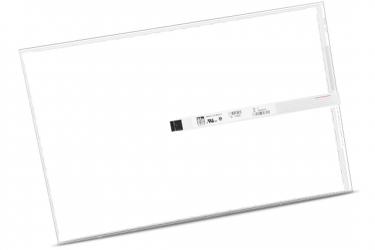
Food plants and touchscreen displays
The benefits of resistive touchscreen panels are best seen in food plants where screens require a high level of sealing and are often activated by people wearing gloves. During breaks in production, the touchscreens of food plants need hosing down to remove excess mess. Technologies that rely on a path to earth through the finger do not cope well in such an environment. However, resistive touchscreens are mechanically activated and therefore do not suffer from being cleaned in a thorough manner. They are also very precise and require minimal calibration and setup.
If you are in the food industry and are in need of some robust and resistive touchscreen panels, Black Cat Displays are here to help. With over 25 years of collective Electro-Mechanical experience, we are well prepared when it comes to designing touchscreen displays for your food production plant. Contact us today for more information.